Force sensors
Advantages of force sensors
- Measuring ranges from 0.1 to 750 kN
- Low linearity deviation despite high forces
- Robust design with small dimensions
- Pressure and tension measurements
- Integration of signal conditioners
- High breaking load range up to 600% / F.S.
- Individual designs and dimensions possible
- Robust steel and aluminum housings
- Sealing up to IP69K for special requirements
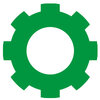
We also modify series types to your individual requirements and wishes.
Operating principle
In strain gauge (DMS) based force sensors from Inelta, static and dynamic tensile and compressive forces are detected by means of special resistors (DMS) and converted into electrical signals. A strain or compression of the strain gauge resistor causes a voltage change. This voltage is proportional to the applied force, which minimally mechanically compresses or stretches the carrier material under the strain gauge.
In order to achieve optimum measured values, 2 or 4 strain gauges are usually applied in force sensors and connected to each other in a bridge circuit (Wheatstone bridge circuit). In this way, undesirable thermal or mechanical influences can be compensated, also called adjustment.
Application
Our force sensors are used in various industries. From medical technology for the exact positioning of diagnostic systems, to force measurement on linear drives in aerospace, to level measurement for the food industry. Our force sensors are also used to determine pretensioning and contact forces in manual devices as well as on test equipment in production.
Structure of force sensor KMT55
![]() | Connection cable |
---|---|
![]() | Cable gland |
![]() | Diaphragm Stainless steel 1.4542 or aluminum EN AW 2024 |
![]() | Strain gauge |
![]() | Electronics/signal conditioner |
![]() | Housing base welded / glued |
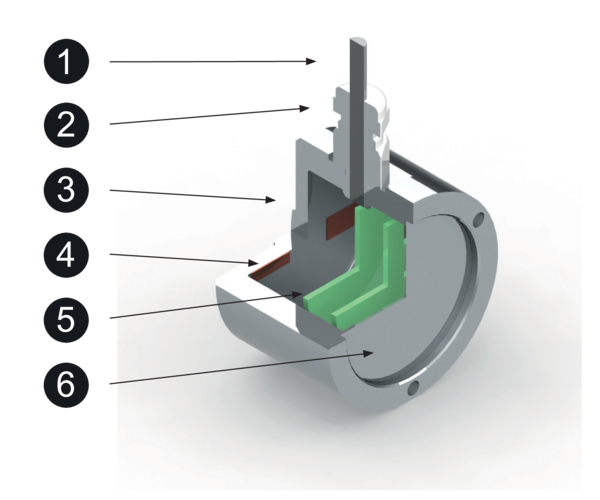